CutAce
Precision plasma cutting with best in class speed and productivity features
Plazmax’s CutAce is the first choice for manufacturers and engineers looking for the most efficient unitised cutting system on the market.

Precision bevelling up to ±50°
19” Touch Control Panel for quick pre-set settings
Turnkey Installation & Training Included
Unrivalled quality
The CutAce line of plasma cutters offer unrivalled cut quality on carbon steel, aluminium and stainless steel utilising Hypertherm’s outstanding power sources, and can be specified with a range of cutting table sizes to suit your needs.
- Precision bevelling up to ±50°
- Best machine in class - more parts, lower cost, greater profit
- Both slats and slat holder system easily removable for cleaning and maintenance
- Easy Camera Plate Alignment
- Quality standardised components readily available and always stocked
- Remote support enabled for help anytime, anywhere
- Fully Integrated Hypertherm software and hardware
- Standalone 19” Touch Screen Console
- Scribing and Oxy-torch compatible

Precision beveling for weld-ready parts
Create parts faster by eliminating secondary weld-prep processes with Plazmax’s industry-leading automatic bevel head. Program advanced bevels and cut angles up to ±50° using the Hypertherm XPR plasma system and integrated TrueBevel technology.
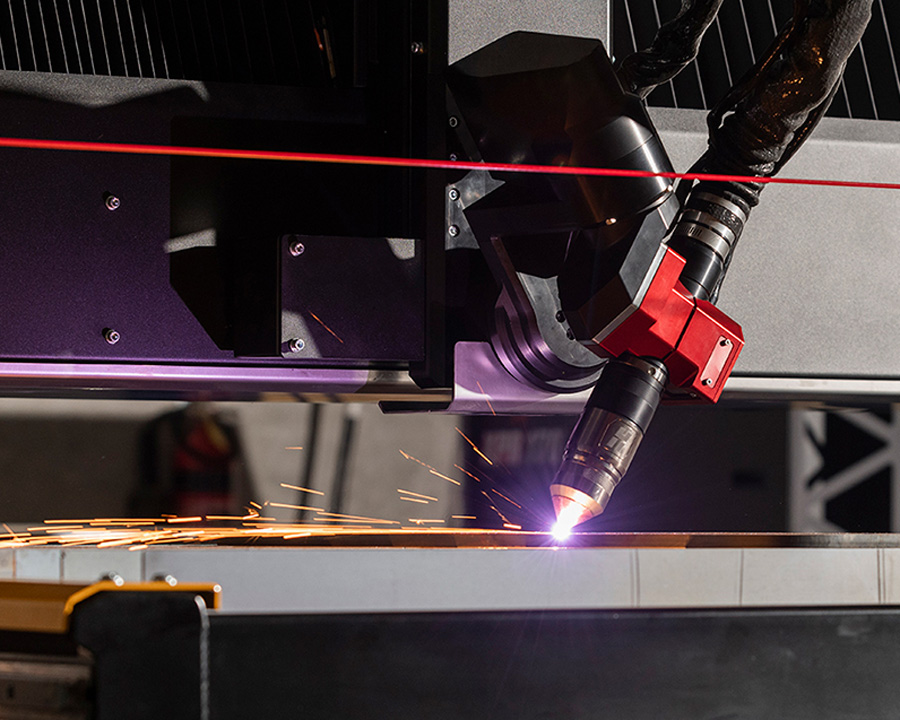
Effortlessly Cut Taper-Free Holes
Plazmax’s groundbreaking ‘MaxControl’ software now enables users to cut taper-free holes below 1:1 ratio. With torch head rotation, create clean straight-walled holes in mild steel, stainless steel, and aluminum down to 8mm on 10mm plate effortlessly.
Absolute control at your fingertips
Plazmax’s custom 19’’ Touch Screen Console makes setting up even complicated tasks a breeze. Its user-friendly interface makes the learning process simple, and with built in real-time remote access you’ll always have the full support of the Plazmax technicians and support team for system diagnostics, troubleshooting and training.

Service & Support
Plazmax offers complete turn-key installation for cutting and robotic systems, providing on-site and remote training for both machines and software. With comprehensive service plans, 24/7 on-call breakdown service and remote diagnostics, you can count on reliable support worldwide.

ProNest® Software
Designed to supercharge your cutting operation, ProNest® CAD/CAM part nesting software will help you achieve greater automation, efficiency, and profitability.
Power Options
The CutAce can be configured and supplied with a choice of Hypertherm power options. Starting with the Hypertherm MaxPro200 for light to medium duty application and working up to the more sophisticated XPR170, 300 and 460 models for more heavy duty tasks and high definition quality cutting.

Hypertherm XPR170

Hypertherm XPR300
Specifications
General
Working Material
- Carbon Steel (up to 64mm)
- Aluminium (up to 63mm)
- Stainless Steel (up to 63mm)
Cutting Table Options
- 3m x 1.5m
- 3.6m x 1.8m
- 6m x 2.5m
- 9m x 2.5m
Technology
Software
- ProNest Nesting Software
- MaxControl CNC Software or / Phoenix CNC Software
Hardware
- 19” Touch Screen Display
Options
Compatible Options
- Oxy-Fuel Cutting
- Bevel Head
- Marking / Scribing
- Downdraft Fume Extraction or Water Table
Power Options
- Hypertherm MaxPro200
- Hypertherm XPR170
- Hypertherm XPR300
- Hypertherm XPR460
Finance Options
Although it’s obvious to most the Return On Investment a high-tech piece of equipment can provide, banks and lenders don’t always understand your industry and the importance of such purchases.
Related Product
Plazmax CutPro
Ultra-heavy-duty CNC plasma cutting system for extreme duty applications
